As the saying goes, you can’t manage what you can’t measure. Today this is true of many
things in warehouse and distribution center management, but perhaps nowhere more so
than for monitoring the productivity of your workforce. Payroll is typically the largest single
expense in the warehouse. Because of this, many companies have undertaken projects to
utilize Warehouse Management Systems (WMS) and other technologies to do more work in
less time. But while directed, verified work direction raises efficiency levels; it is not enough
to truly streamline work performed and maximize your dollars spent.
The fact is many businesses fail to gain visibility to the work their employees carry out on a
daily basis. They balance the need to meet tight customer deadlines with making sure
employees are on time for work. This is a difficult challenge. Fortunately, the advent of labor
management systems (LMS) has enabled businesses to better use labor resources, maintain
profit margin expectations and gain a competitive edge. Many businesses are looking to
these systems as a foundation for improved workforce management and cost reduction—
whether they already have a WMS or not. Labor management has become the next logical
step for businesses in search of new efficiencies.
Five Reasons You Cannot Afford to Postpone Your Labor Management Project
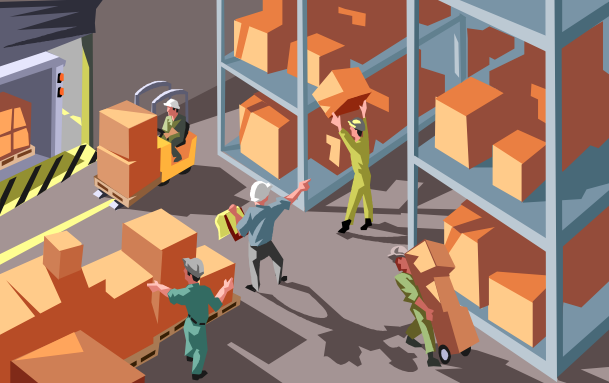